If you place your mechanical arm between rows 4
and 5
or between columns e
and d
, the furthest point you have to reach would be sqrt(14^2 + (28+6)^2), which evaluates into 36.77cm, and I would say 2 pieces of 20cm would be almost enough, but just to be safe, I'd make 'em both 25cm and you may put it anywhere within 6cm from the board.
Material choice. Acrylic is very fragile and prone to cracking. The weight of the largest chess piece + the weight of all machinery (actuators, magnets, etc.) will easily crack it after a while. Use a more durable plastic instead.
Design choice. The arm you describe would be quite difficult to control, you have to move both joints at the same time with the different speeds, and if you miss and knock another piece off the board -- you lose the game. For speed-independent precise positioning I'd use X-Y table, something like this picture, where X and Y motions can be totally independent, precision is very high and you may easily put a few kilograms of equipment on the top and it will work.
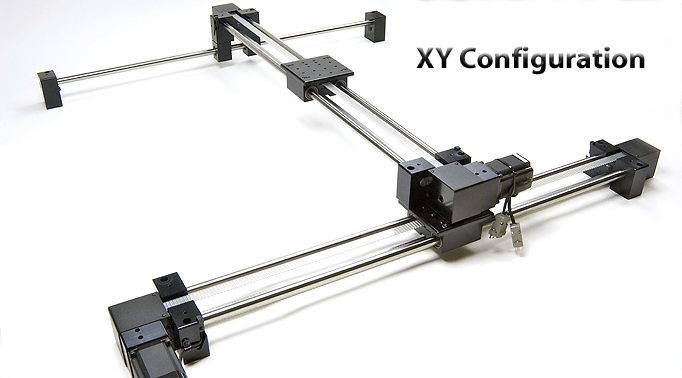